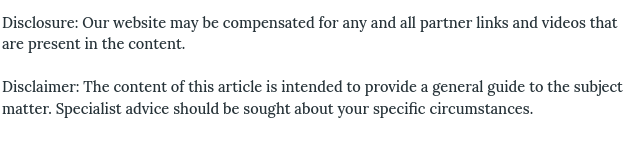

This article is all about boring heads, boring inserts, and boring tools. And by boring, I do not mean dull! I mean “boring” in the sense of an internal diameter counterpart to “turning,” which is the process of cutting external diameters. Boring serves a very important purpose, which is to achieve the highest level of accuracy possible of the diameter of a hole.
Boring and turning are often referred to as being inseparable from one another. However, this is a misnomer. Boring is its own category of machining because it is intrinsically more difficult to do than turning is. This is also true of boring inserts versus turning inserts.
In boring and boring inserts, the surface finish, otherwise known as roughness, can be anywhere in the range of 8 to 250 microinches. However, more often than not, the surface finish is between 32 and 125 microinches.
Although there are many different kinds of workholding devices that can be utilized for borers and boring inserts, the three most commonly used workholding devices are the faceplate, the three jaw chuck, and the four jaw chuck. These are typically used with a lathe. The correct workholding device is dependent on the circumstances of use and varies according to the situation.